easily calculate compressed air cost
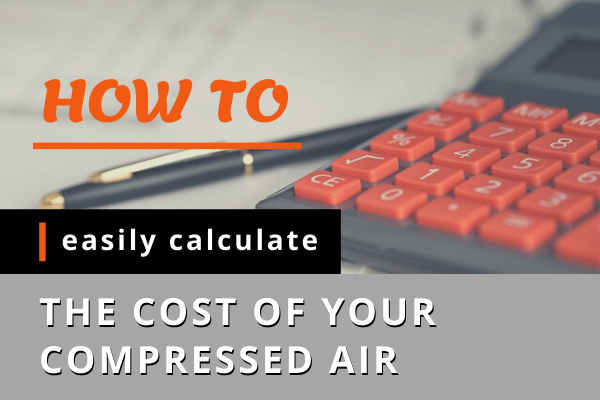
This article not only touches on how to calculate the cost of compressed air based on electricity cost alone but also the actual cost once heat recovery is integrated. If you would like to calculate compressed air cost based on electricity alone please refer to the below compressed air cost calculator and example.
Most industrial facilities use compressed air, whether it’s for running air tools, pneumatic controls for conveying, cooling and blow off. A survey by the U.S. Department of Energy (DOE) shows that for a typical industrial facility, approximately 10% of the electricity consumed goes to generating compressed air. This is a significant amount – therefore knowing the cost of this compressed air is important.
For some manufacturing facilities, the cost of compressed air generation may account for 30% or more of the electricity consumed in the plant. Some companies use a value of 30 cents to 50 cents per 1,000 cubic feet of air as an estimate but in reality actual cost can vary greatly. Air compressors are considered notoriously inefficient when looked at as a separate entity. However, the real cost should also take into consideration the recovery of waste heat generated by the heat of compression. The heat of compression is the heat generated when air is compressed. It is removed using intercoolers between compressions stages and again using an aftercooler at the end of the compression cycles.
If this waste heat is used for the production process, or to heat the premises, it is possible to achieve impressive efficiencies of well over 90 percent. In fact, of the 100 percent of the electrical energy consumed, some 94 percent is converted to heat, that can be put to good use after it has been recovered. This does not actually make compressed air cheaper per cubic meter to produce, but there are significant savings when this waste heat is used for other purposes such heating buildings or water.
The lifetime cost of compressed air excluding heat recovery consists of:
- Equipment and Installation Cost – about 12%
- Maintenance Cost – about 12%
- Electricity Cost – about 76%
However, the cost of compressed air is usually taken as only the electrical cost. Considering that alone (and not the other costs and not the recovered cost from using waste heat), provides the usual daily usage cost of compressed air. The overall efficiency of a typical compressed air system can be as low as 10% to 15%. For example, to operate a 1-hp air motor at 100 psig, approximately 7 to 8 hp of electrical power is supplied to the air compressor.
To calculate the cost of compressed air based on electrical cost alone, use the following formula:
Variables:
- hpb = compressor shaft horsepower (often higher than the motor nameplate horsepower and can be checked under the equipment specification)
- Percent time = percentage of time running at this operating level,
- Percent full-load hpb = hpb as percentage of full-load hpb at this operating level, and
- Motor efficiency = Efficiency of the electric motor at this operating level.
Calculation Example
A typical manufacturing facility has a 100 hp compressor (which requires 110 hpb) that operates for 7,000 hr annually. It is fully loaded 85% of the time (motor efficiency is 95%) and unloaded the rest of the time (25% full-load hpb and motor efficiency is 90%). The aggregate electric rate is $0.10/kWhr.
- Calculate the cost when fully loaded:
((110 hp) X (0.746) X (7,000 hr) X ($0.10/kw-hr) X (0.85) X (1.0))/.95 = $51.396.00 - Calculate the cost when partially loaded:
((110 hp) X (0.746) X (7,000 hr) X ($0.10/kw-hr)X (0.15) X (0.25))/.90 = $2393.00 - Annual energy cost = $51,396.00 + $2393.00 = $53,789.00
Note: The general rule to approximate performance of a compressor is about 4 to 4.5 SCFM/Hp. So using an average of 4.25 SCFM/HP a 100 HP compressor will produce 425 SCFM.
For 7000 hours of operation the cost per 1000 cubic feet in this case would be:
$53,789/(425 SCFM X 7000 hr. X 60 Minutes/hr.) X 1000 cubic feet) = $0.30 / 1000 cubic feet.
But…. what if there is heat recovery?
Can Compressors Actually be Energy Savers?
Chemical and food processing operations use temperature controlled processes and have a year-round requirement for heat.
Paint shops and electroplating operations also need a constant supply of heat for their processes. In plants that do not require process heat, the user has the choice between either heating the premises or heating water.
Modern water-cooled compressors are easily integrated into a heat recovery system. There are a lot of much older compressor stations, though, that work without heat recovery. For stations such as these, there are many systems on the market that can be purchased to utilize heat recovery. This turns the compressor into an “energy saver” with a surge in overall efficiency, no matter what the original model or output was.
The investment costs for a heat recovery systems depend largely on the structural conditions at the site but paybacks are usually under a year.
Air-cooled systems can use the exhaust air to heat rooms or production facilities. This can also be very easily achieved using the outdoor thermostat control. In this case, from a defined temperature upwards, the exhaust air stream from the sound insulation hood is switched over to heat the production facility when temperatures drop – and all this comes at no extra cost.
So what is the “real” cost of compressed air. If there is a heat recovery system. Let’s assume the heat recovery system saves even a small amount – say $10,000.00 a year. Then the $53,789.00 cost is really $43,789.00 because we can utilize the heat byproduct.
The cost per 1000 cubic feet reduces to: $0.245/1000 cubic feet which is quite dramatic.
Considering that compressed air operated equipment tends to be more rugged, simpler and that compressed air operated equipment compared to hydraulic or electrical equipment is safer, faster and more user friendly, the real cost of using compressed air is not just the electricity that runs the air compressor. You need to take into account many other factors such as heat recovery, and the maintenance costs and uses of the compressed air operated equipment itself.
Conclusion
In view of low investment, compressed air users should seriously consider the option of utilizing waste heat. Even a relatively small , 25 hp compressor provides enough waste heat to keep a domestic dwelling warm. It is also a good idea to look into the fine tuning of other factors involved in the efficiency of compressed air supply. These include recommendations on the pressure level, optimizing the regulation with as low a pressure range as possible, the use of variable speed compressors for peak loads, and reducing inefficient idle times. Regular leak testing, which can also be achieved electronically by modern control systems, through measuring the drop in pressure when the compressors are switched off, then using a leak detector to find leaks and fix them.